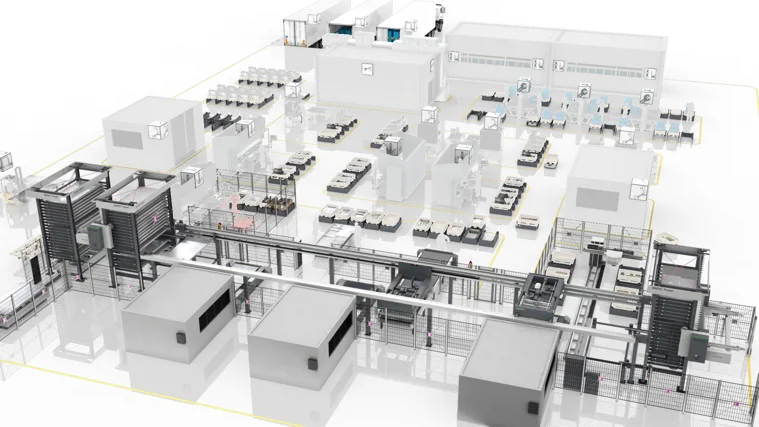
Coraz więcej przedsiębiorstw odkrywa korzyści wynikające ze zautomatyzowanego przepływu materiału i w związku z tym postanawia na nowo ukształtować swoje wewnętrzne procesy logistyczne. Można jednak zauważyć, że często brane są pod uwagę tylko poszczególne miejsca przepływu materiału, a nie cały proces – począwszy od dostawy surowców aż po wysyłkę własnych produktów. Ekspert w zakresie obróbki materiału, firma Remmert, przygotowała wskazówki dla przedsiębiorców zajmujących się obróbką metalu, w jaki sposób można zoptymalizować procesy związane z przepływem towarów, aby trwale zwiększyć wydajność i produktywność.
1. Szukanie możliwości optymalizacji w obrębie przepływu towarów
Jeśli chce się efektywnie włączyć automatyzację w procesy, powinno się wziąć pod lupę kompletny przebieg, począwszy od dostawy towarów. W wielu przedsiębiorstwach już w pierwszych etapach pojawia się potrzeba optymalizacji: często dostarczony materiał jest najpierw odkładany bez planu i w nieokreślonym czasie umieszczany w magazynie, tam gdzie akurat jest miejsce. Przechowywanie na podłodze nie jest jednak najodpowiedniejszą metodą, zapewniającą wydajny przepływ materiału. Zamiast tego zaleca się indywidualne przyjrzenie się każdemu możliwemu systemowi magazynowemu, by dowiedzieć się, jaki typ magazynu pasuje najlepiej do miejsca dostawy, materiału, jak i do kolejnych kroków w zakresie obróbki. Główna zasada brzmi: czas między dostawą a magazynowaniem powinien być jak najkrótszy. Aby osiągnąć optymalny przepływ materiału każdy towar do składowania, podczas dostawy powinien być przekazywany na nośnik magazynowy, który bezpośrednio i automatycznie jedzie na swoje miejsce. Kolejnym decydującym aspektem, w którym tkwi potencjał optymalizacyjny, jest wykorzystanie dostępnego miejsca. Planując, zaleca się dopasowanie automatycznych rozwiązań do miejscowych warunków. Najważniejszy punkt w tym kontekście: optymalizacja podłączenia maszyn. Bardzo często istniejące urządzenia nie są zintegrowane z procesami w taki sposób, aby współdziałając osiągały możliwie najlepsze rezultaty. Jest tak przede wszystkim tam, gdzie utrzymuje się konwencjonalne sposoby postępowania i tradycyjne koncepcje przepływu materiału, mimo że nie sprzyjają już one produkcji. W takim przypadku przedsiębiorstwa powinny pilnie wdrożyć nową koncepcję przepływu materiału.
Możliwość integracji maszyn obróbczych, niezależnie od producenta, już podczas fazy planowania, zapewnia użytkownikowi najwyższą elastyczność. Na uwagę zasługują w tym przypadku specyficzne wymagania przedsiębiorstwa i produkcji. Klienci wybierają pasującą im maszynę, a eksperci w zakresie obróbki materiału, tacy jak np. Remmert, zapewniają jej bezproblemowe podłączenie. Kolejna korzyść integracji niezależnej od producenta: absolutna pewność w przyszłości. Zarówno wymiana maszyny, jak i rozbudowa urządzenia mogą zostać zrealizowane w sposób modułowy. Tym samym, w dowolnym czasie można dostosować urządzenie do aktualnych wymogów produkcji.
2. Wybór stopnia automatyzacji
Czy to wykrawarki, lasery, czy piły do cięcia dłużyc, czy też systemy laserowe do cięcia rur – surowce muszą być szybko i wydajnie pobierane z magazynu i transportowane do dalszej obróbki. Przy tym istotne jest, aby jak najlepiej wykorzystać maszyny, bez możliwych przestojów. Pojedyncza kontrola zapewnia określenie stopnia automatyzacji (pełnego lub połowicznego) i dodanie odpowiednich rozwiązań do istniejącego przepływu materiału. Jednostki automatyczne, które można elastycznie włączyć i zintegrować niezależnie od producenta, oferują możliwość dopasowania urządzenia do aktualnych warunków i odpowiedniej rozbudowy, również w przyszłości. Także tutaj na pierwszym planie są specyficzne dla klienta wymagania i cele, tak samo jak wybór dostosowanych rozwiązań, które mogą pracować w pełni automatycznie lub też elastycznie - jako w połowie zautomatyzowane. Poprzez zastosowanie komponentów modułowych, jak na przykład rodzina FLEX firmy Remmert, urządzenia można łatwo rozbudowywać. Dzięki temu rozwiązanie przepływu materiału może rosnąć w zakresie wydajności i stopnia automatyzacji.
3. Wybór najlepszego typu magazynu dla materiału i produkcji
Jaki typ magazynu najlepiej nadaje się do konkretnych warunków na miejscu, wynika najczęściej już z pierwszej rozmowy dotyczącej planowania i postawionego celu przez klienta. Decydującymi zmiennymi są: ilość towarów magazynowych, istniejące pomieszczenie magazynowe i zapotrzebowanie na materiał do produkcji. Te czynniki wyznaczają wielkość magazynu i wymaganą prędkość rozwiązań automatyzacji. Ponadto należy uwzględnić, jak materiały mają być następnie dalej obrabiane. Jeśli przykładowo, podłączana jest maszyna do produkcji, magazyn powinien umożliwiać zastosowanie w połowie lub w pełni automatycznego rozwiązania.
4. Określenie przyszłych oczekiwań i wsłuchanie się w rady eksperta
Jeśli dane biznesowe i wskaźniki wydajności nie odzwierciedlają pożądanych wyników, opłaca się zazwyczaj przegląd całkowitego przepływu materiału. Wiele możliwych problemów łączy się z tym, że przedsiębiorstwa nie przywiązują wystarczającej uwagi do intralogistyki.
„Temat przepływu materiału po dokładnym przyjrzeniu się okazuje się nad wyraz kompleksowy”, wyjaśnia Frank Baudach, kierownik ds. sprzedaży dla krajów niemieckojęzycznych i Beneluksu w firmie Remmert. „Przedsiębiorstwom opłaca się zatem doradztwo ekspertów z know-how w zakresie wymogów dotyczących różnych materiałów. Wspieramy przy tym naszych klientów planowaniem, analizami korzyści i kosztów oraz spojrzeniem w przyszłość pod kątem znalezienia dopasowanych rozwiązań, tak aby oszczędzić czas i wydatki. Przy tym pracujemy kompleksowo i dzięki temu oferujemy naszym klientom wszystkie konieczne usługi, począwszy od doradztwa, poprzez realizację i długotrwały serwis w jednym miejscu.”
Efektywność procesu czynnikiem sukcesu: Dzięki kompleksowej koncepcji przepływu materiału można istotnie zwiększyć wydajność produkcji.
Jaki typ magazynu najlepiej nadaje się do konkretnych warunków na miejscu, wynika najczęściej już z pierwszej rozmowy dotyczącej planowania i postawionego celu przez klienta.
źródło: Remmert