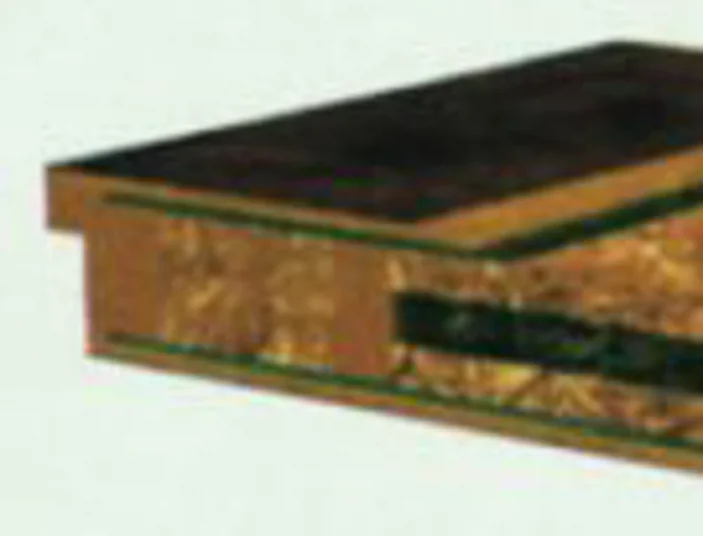
|
|
|
|
|
|
|
|
|
Tradycyjnym materiałem służącym do wykonywania ościeżnic i skrzydeł drzwiowych jest drewno. Przez wieki z powodzeniem stosowano różne jego gatunki. W zależności od dostępności surowca, wykorzystywano zarówno drewno z liściastych, jak i iglastych odmian drzew. Lasy zapewniały możliwość pozyskania drewna wysokiej jakości. O klasie stolarki otworowej decydował sposób obrobienia drewna, układ konstrukcyjny skrzydła i jakość zastosowanych okuć.
Obecnie, pozyskanie surowca drzewnego dobrej jakości, jest sprawą coraz trudniejszą. Zasoby leśne skurczyły się w znacznym stopniu, a nowe lasy , często monokulturowe nie są w stanie dostarczać drewna o parametrach koniecznych do wykonywania doborowych jakościowo elementów stolarki. Podobne problemy spowodowała zachowanie reżymu technologicznego podczas obróbki drewna, zapewniającego zachowanie właściwości i wymiarów podczas eksploatacji. Brak dostępności dobrego jakościowo drewna należało zastąpić innymi materiałami o zbliżonych właściwościach. Stąd już w latach trzydziestych ubiegłego wieku rozpoczęły się próby stosowania zastępczych materiałów drewnopochodnych. Początkowo, problem był wysoki koszt produkcji, wynikający z niskoefektywnych technologii i ograniczonej produkcji koniecznych substancji chemicznych.
O upowszechnieniu materiałów drewnopochodnych zadecydował więc rozwój technologiczny i rozwój kilku dziedzin nauki , ale przede wszystkim chemii i mechaniki.
Obecnie drzwi wewnętrzne wykonane całkowicie z drewna stanowią nieznaczny, ekskluzywny i co za tym idzie drogi, odsetek produkcji.
W produkcji masowej przez dwie, trzy dekady łączono drewniane ramiaki , wykonane z drewna niskiej jakości (często z oflisami, ubytkami sęcznymi), z płycinami wykonanymi z twardych odmian płyt pilśniowych. Obecnie także w konstrukcjach drzwi wyższej jakości powszechnie wykorzystuje się surowce drewnopochodne. Pewnym standardem stały się wypełnienia drzwi wykonane z płyt wiórowych lub wypełnienia płycin z porowatych płyt pilśniowych.
Płyty pilśniowe produkowane są z masy uzyskanej z rozwłóknionej tkanki drzewnej. Przygotowana masa poddawana jest spilśnieniu (rozdzieleniu masy drzewnej na pojedyncze włókna i zmianie kierunku przebiegu włókien) i uformowaniu w płyty. Obecnie do produkcji płyt pilśniowych stosowane są trzy technologie. Płyty twarde wytwarzane są w technologii suchej , tzw. MDF (w niej obecnie obserwuje się największy postęp technologiczny) oraz w technologii mokrej przez prasowanie w podwyższonej temperaturze pod wysokim ciśnieniem prasy. Płyty pilśniowe miękkie (porowate) produkowane są w technologii prasowania na mokro . do masy drzewnej dodawane są składniki przeciw pleśniowe lub hydrofobizujące. Do produkcji elementów stolarki drzwiowej wykorzystuje się wszystkie rodzaje płyt pilśniowych.
- Płyty twarde-(HB) charakteryzują się gęstością powyżej 800 kg/m 3. Dostarczane są do producentów stolarki z wilgotnością własną 5-9%. Do produkcji drzwi znajdują zastosowanie płyty o grubości 2,4 ;3,2 ;4,0 i5 ,0 mm. Ich podstawową zaletą jest wysoka wytrzymałość na zginanie statyczne, która zależnie od grubości płyty wynosi od 32 do 35 MPa. Twarde i półtwarde płyty pilśniowe charakteryzuje duża sztywność, wytrzymałość i jednorodna struktura. Niestety płyty pilśniowe twarde maja także wady. Podstawowa to wysoka nasiąkliwość w przypadku zamoczenia (25 – 40%) oraz będące jej skutkiem spęcznienie płyt (20-30%). Twarde płyty pilśniowe znajdują zastosowanie do wykonania powierzchni zewnętrznych drzwi płytowych. Często oklejane są foliami imitującymi strukturę i kolor drewna czyli płyty twarde laminowane (typ T). Ich powierzchnia gładka, licowa została fabrycznie (w procesie produkcji) pokryta cienką warstwą tworzywa sztucznego przez naprasowanie folii melaminowo- formaldehydowych. Stosowane powszechnie folie posiadają strukturę imitującą wzory słoi drewna. Podobnie odpowiadają kolorom naturalnego lub barwionego lazurami drewna. Występują w wariancie z pół połyskiem lub są matowe. Płyty pilśniowe twarde wytwarzane są także jako lakierowane- są to płyty pilśniowe o powierzchni licowej zabezpieczonej powłokami lakierów termoutwardzalnych.
- Płyty pilśniowe porowate (SB) wytwarzane są z pilśni drzewnej, często z dodatkiem włókien lnu lub spilśnionych włókien konopi. Dostarczane są do producenta w stanie wilgotności własnej do 12%. Zaletą płyt porowatych jest dobra izolacyjność dźwiękowa i termiczna oraz mała gęstość 300-350 kg/m 3. Powoduje ona wysoką podatność materiału na obróbkę plastyczną. Stąd płyty porowate dają się łatwo formować pod ciśnieniem. Ich parametry wytrzymałościowe są mniej imponujące niż płyt twardych. I tak, porowate płyty pilśniowe charakteryzują się wytrzymałością na zginanie statyczne od 0,8 do1,8MPa, w zależności od grubości elementu. Oprócz tego mają kilka wad. Główna to stosunkowo wysoka nasiąkliwość od 30 do 80 %. Oznacza ona, że płyty pilśniowe nie mogą być narażone na zmoczenie wodą. Dlatego znajdują one zastosowanie jako wypełnienia drzwi płytowych wewnętrznych (poprawa izolacyjności akustycznej skrzydła) oraz jako wypełnienia prasowanych (tzw. sandwitsh), prefabrykowanych płycin drzwi wewnętrznych. Płyty pilśniowe porowate produkowane są o grubościach : 9,5;12,0; 16,0;19,0 mm.
Płyty wiórowe .
Innym produktem drewnopochodnym szeroko stosowanym w produkcji drzwi wewnętrznych są płyty wiórowe. Powstają one w efekcie łączenia w prasach wiórów suszonych i wymieszanych lub nasączanych klejem (spoiwem formalhetydowym lub rzadziej mocznikowym). Wióry konieczne do wytworzenia tego rodzaju płyt uzyskuje się w tzw. rębakach z odpadów drzewnych powstających w czasie produkcji z drewna litego np. podczas pracy łuszczarek lub korowarek. Do produkcji drzwi wewnętrznych stosowane są płyty wiórowe kanałowe o grubości 35 mm (średnica kanału 22 mm) i płyty o grubości 38 mm i kanałach o średnicy 25 mm. Płyty stanowią wypełnienie drzwi i każda ich krawędź boczna łączona jest klejowo z ramiakiem drzwi, zwykle wykonanym z drewna litego lub klejonego. W tanich odmianach drzwi wewnętrznych spotyka się ramiaki wykonane z frezowanej płyty wiórowej pełnej. Ponadto płyty wiórowe znajdują zastosowanie do wykonywanie drzwi płytowych wytłaczanych lub drzwi frezowanych. Wynika to z dobrej obrabialności płyt wiórowych pełnych.
Rozróżnia się płyty płasko prasowane i płyty wytłaczane pełne. Oba typy płyt wiórowych produkowane są w kilku grubościach: 15,16,17,18, 19, 25, 38 mm.
Płyty płasko prasowane i płyty wiórowe wytłaczane, produkowane są w odmianie :
-płyty pełne ,
-płyty pustakowe –(kanałowe) posiadające otwory o przebiegu liniowym wzdłuż osi wzdłużnej płyty.
Płyty wiórowe charakteryzują się gęstością od 700 do 900 kg/m 3 . Dostarczane są do producentów stolarki drzwiowej w wilgotności nie przekraczającej 8%. Oprócz tego płyty wiórowe wykazują wysoka odporność mechaniczną. Ich wytrzymałość na zginanie statyczne wynosi zależnie od kierunku działania siły zginającej w stosunku do kierunku wytłaczania od 6 do 34 MPa. W zależności od metody obróbki , płyty mogą być szlifowane lub nie szlifowane. Płyty wiórowe doskonale nadają się do obłogowania lub okleinowania.
Sklejka.
Sklejka otrzymywana jest przez sklejanie w prasie fornirów skrawanych obwodowo o grubości 0,1- 3,5 mm z drewna drzew iglastych lub liściastych. Dzięki poprzecznemu układowi przebiegu słojów w kolejnych warstwach sklejki, jej parametry wytrzymałościowe w stosunku do drewna litego o tej samej grubości, ulęgają znacznemu wzrostowi. Ilość warstw w sklejce jest zawsze nieparzysta. Poszczególne warstwy sklejki łączone są klejami mocznikowymi lub formaldehydowo- fenolowymi. Sklejki wykorzystuje się do produkcji pokryć drzwi płytowych, wytwarzania płycin drzwi płycinowych lub do wykonywania ramiaków lub części usztywniających w drzwiach wewnętrznych. Sklejki o małych grubościach (trzy warstwowe) są podatne na wytłaczanie w specjalnych prasach.
Do stolarki drzwiowej znajdują zastosowanie dwa rodzaje sklejek :
- cienkowarstwowe o grubości < 2 mm
- grubowarstwowa o grubości >2mm .
„Koszule”, czyli warstwy licowe sklejek wykonywane są z fornirów sosnowych, brzozowych lub bukowych.
W zależności od odporności na działanie wody rozróżnia się trzy typy sklejek:
- suchotrwałą – S
- pólwodoodporną – W 1
- wodoodporną – W 2
Do produkcji stolarki wewnętrznej stosowana jest zwykle sklejka pólwodoodporna.
Pod względem jakości wykończenia powierzchni płyt rozróżnia się sklejkę szlifowaną i nieszlifowaną.
Forniry
Stanowią rodzaj okleiny naturalnej. Produkowane są na łuszczarkach przez skrawania z drewna litego. Grubość wysuszonych fornirów wynosi od 0,5 do ok. 1,5 mm. Forniry mogą być skrawane obwodowo lub mimośrodowa. W zależności od sposobu ich uzyskiwania możliwe jest składanie fornirów w sposób pozwalający na uzyskanie różnego rodzaju rysunku słojów drewna. Forniry nakleja się na elementy drewnopochodne np. płyty wiórowe, twarde płyty pilśniowe lub sklejki. Stosowanie fornirów do produkcji stolarki drzwiowej wewnętrznej ograniczone jest do produktów wysokiej jakości. Układ słojów pozwala na imitowanie drzwi wykonanych z litego drewna( drzwi płytowych). Forniry znajdują także zastosowanie do produkcji płycin drzwiowych . Obecnie stosowane są forniry uzyskane ze skrawania zarówno odmian drzew występującej w naszym kraju (dębu, buka, sosny, olchy), ale także z drzew egzotycznych (mahoniu i in.).
W celu ochrony lub uzyskania pożądanego koloru gotowy element drzwi pokrytych okleina naturalną jest zabezpieczany przez pokrywanie lazurem lub lakierem.
W produkcji przemysłowej, coraz częściej są wypierane przez powłoki (filmy) melaminowe, tańsze w produkcji i mniej kłopotliwe w przypadku pokrywania powierzchni płyt drzwiowych.
Obecnie materiały drewnopochodne stanowią podstawowy zestaw surowców stosowanych do produkcji drzwi wewnętrznych. O ich upowszechnieniu zadecydowały, oprócz problemów z surowcem drzewnym dostępnym w dostatecznej ilości także względy ekonomiczne. Materiały drewnopochodne nie wymagają długotrwałego suszenia i obróbki prowadzącej do powstania odpadów. Często same produkowane są z odpadów drzewnych. Pozwalają na wykorzystanie deficytowego surowca w sposób całkowity. Jednocześnie charakteryzują się dobrymi parametrami w zakresie swojej wytrzymałości mechanicznej i są materiałami łatwo obrabialnymi.
Piotr Wierzelewski